Hybrid Furnaces: Revolutionizing Glass Melting with 80% Renewable Energy
The glass industry accounts for approximately 2.6% of global industrial CO₂ emissions. As the world intensifies its focus on sustainability, the glass manufacturing sector is under increasing pressure to reduce its carbon footprint. Enter hybrid furnaces—a groundbreaking innovation poised to transform glass melting by utilizing up to 80% renewable energy.
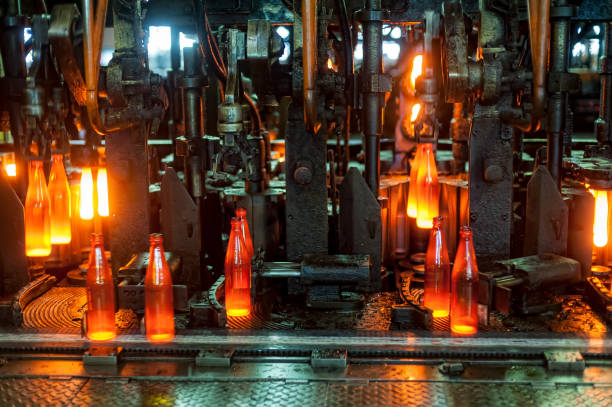
The Evolution of Glass Melting Technology
Traditional glass melting relies heavily on fossil fuels, primarily natural gas, leading to significant greenhouse gas emissions. While incremental improvements have been made over the years, the fundamental process has remained largely unchanged—until now. Hybrid furnaces represent a paradigm shift, combining electrical energy with conventional fuel sources to achieve more sustainable operations.
Revolutionizing Glass Melting with 80% Renewable Energy
Hybrid furnaces are designed to operate predominantly on renewable electricity, with the capability to use up to 80% green energy. This substantial reduction in fossil fuel dependency not only decreases CO₂ emissions but also aligns with global efforts to transition towards cleaner energy sources. By integrating electric heating elements into traditional furnace designs, manufacturers can achieve precise temperature control and improved energy efficiency.
The adoption of hybrid furnaces is more than just an environmental statement; it’s a strategic move towards future-proofing the glass industry. As renewable energy becomes more accessible and cost-effective, leveraging such technologies ensures compliance with tightening environmental regulations and meets the growing consumer demand for sustainable products.
Case Study: Libbey Glass’s Commitment to Sustainability
A notable example within the Glass Manufacturing Industry Council (GMIC) is Libbey Glass. The company has embarked on a Flexible Fuel Electric Hybrid Glass Furnace Demonstration Project aimed at replacing four regenerative furnaces with two larger hybrid electric furnaces. This initiative is projected to reduce approximately 60% of carbon dioxide emissions at Libbey’s facility in Toledo, Ohio. The hybrid furnaces combine the benefits of oxygen fuel with electric melting, replacing up to 80% of the melting energy with renewable-sourced electricity. This project not only underscores Libbey’s dedication to environmental stewardship but also sets a precedent for the entire glass industry. Read more about the project here.
Benefits Beyond Emission Reduction
The advantages of hybrid furnaces extend beyond lowering carbon emissions:
- Energy Efficiency: The integration of electric heating allows for more precise temperature control, leading to optimized energy consumption.
- Operational Flexibility: Hybrid systems can switch between energy sources based on availability and cost, providing manufacturers with greater adaptability.
- Enhanced Product Quality: Improved temperature regulation contributes to consistent glass quality and reduces defects.
- Cost Savings: Over time, reduced energy consumption and potential incentives for using renewable energy can lead to significant financial benefits.
Industry-Wide Adoption and Collaborative Efforts
The transition to hybrid furnaces is gaining momentum globally. For instance, a consortium of 20 European glass container producers has initiated the “Furnace of the Future” project. This collaborative effort aims to construct the first large-scale hybrid electric furnace capable of processing over 300 tonnes of glass per day using up to 80% renewable electricity. Such initiatives highlight the industry’s collective commitment to sustainable innovation. Glass Global
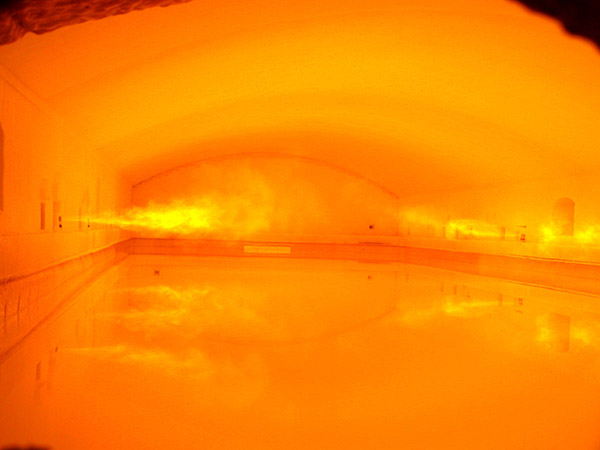
Challenges and Considerations
While the benefits are compelling, the adoption of hybrid furnaces is not without challenges:
- Initial Investment: The upfront costs for developing and installing hybrid systems can be substantial.
- Infrastructure Requirements: Adequate access to renewable electricity and grid capacity is essential for optimal operation.
- Technical Expertise: Implementing and maintaining hybrid systems necessitates specialized knowledge and training.
Addressing these challenges requires coordinated efforts among manufacturers, policymakers, and energy providers to create an enabling environment for sustainable technologies.
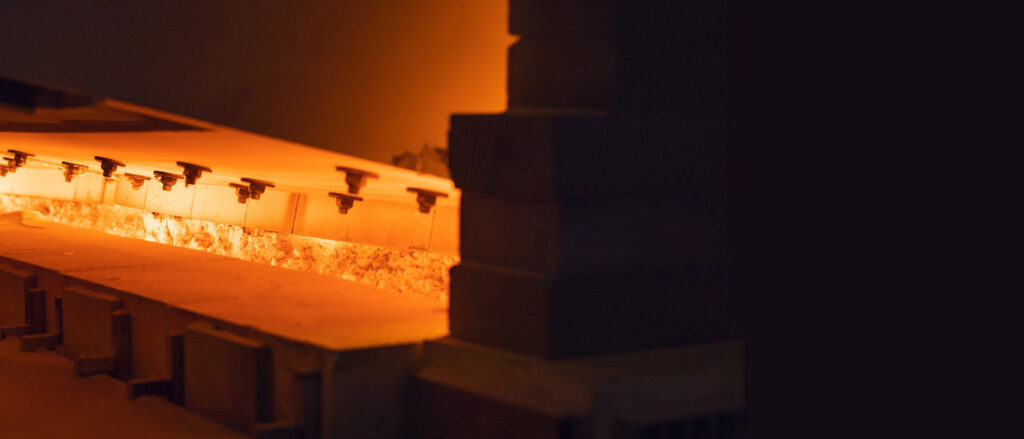
The Road Ahead: Embracing Sustainable Innovation
As we look to the future, the role of hybrid furnaces in revolutionizing glass melting with 80% renewable energy cannot be overstated. Embracing this technology is not merely an environmental imperative but a strategic necessity for the glass manufacturing industry. By investing in hybrid furnaces, companies position themselves at the forefront of innovation, ready to meet the demands of a sustainability-conscious market.
At the Glass Manufacturing Industry Council (GMIC), we are committed to supporting our members in this transformative journey. Through collaborative initiatives, knowledge sharing, and advocacy, we aim to facilitate the widespread adoption of technologies that pave the way for a greener, more sustainable future in glass manufacturing.