Optimizing Glass Furnace Operations: CelSian’s Energy-Saving Technologies Aligned with DOE Initiatives
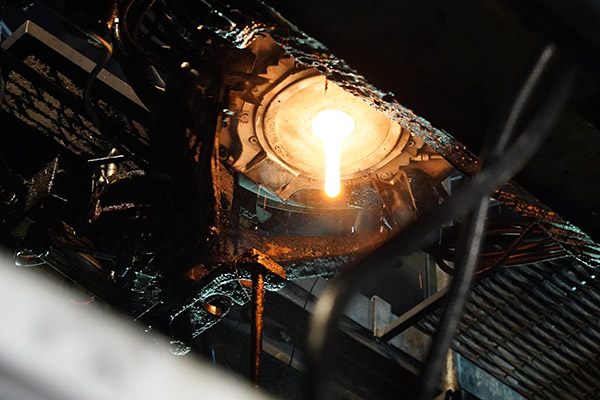
Energy costs can account for up to 14% of total glass production expenses? In an industry where margins are tight, optimizing energy efficiency isn’t just beneficial—it’s essential. The U.S. glass industry faces ongoing challenges in reducing energy consumption while maintaining production quality. This blog explores how CelSian’s Energy-Saving Technologies are transforming glass furnace operations, aligning seamlessly with the U.S. Department of Energy’s (DOE) initiatives to promote sustainability and efficiency.
Understanding the Energy Challenges in Glass Manufacturing
Glass production is highly energy-intensive, requiring extreme heat to melt raw materials into a usable form. The industry’s reliance on high-temperature furnaces leads to substantial energy costs and environmental impact. In response, the DOE has introduced programs to support energy-efficient technologies and workforce training, helping manufacturers lower emissions while improving productivity.
CelSian’s Energy-Saving Technologies: Pioneering Sustainable Solutions
At the forefront of energy optimization in glass manufacturing is CelSian, a company dedicated to providing cutting-edge solutions for furnace operations. Their comprehensive approach includes advanced software, real-time monitoring systems, and workforce training to help manufacturers achieve greater efficiency.
1. Advanced Furnace Modeling (GTM-X)
CelSian’s GTM-X software allows glass manufacturers to simulate furnace operations and identify energy inefficiencies before making costly changes. This predictive modeling tool optimizes combustion, reduces energy waste, and enhances furnace longevity.
2. Specialized Training Programs
Recognizing that technology is only as effective as the people using it, CelSian offers industry-leading training. Their programs, such as the General Glass Technology Training, have educated thousands of professionals in best practices for energy-efficient glass production.
CelSian’s Role in DOE’s ISEED Initiative
The U.S. Department of Energy (DOE) has launched the Industrial Sustainability, Energy Efficiency, and Decarbonization (ISEED) Collaborative, a $3.6 million initiative aimed at improving industrial energy efficiency. CelSian Glass USA was selected as one of only six organizations to participate.
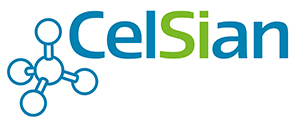
Over the next two years, CelSian will receive DOE funding and technical support to develop and expand specialized training programs that focus on energy efficiency in glass-melting furnaces. These courses include:
- Hands-On Hot Repair
- Oxy-Fuel Furnace Operations
- Sustainable Furnace Operations
These initiatives will not only improve energy efficiency but also create career pathways in the glass manufacturing sector, supporting workforce development across the U.S. By 2025, these programs will be integrated into a national training platform for the industry.
For more details, read the full Glass International article here.
Why This Matters for Glass Manufacturers
For glass manufacturers, adopting energy-efficient technologies is no longer optional—it’s a competitive necessity. By leveraging CelSian’s energy-saving technologies, companies can:
✔ Lower energy costs by optimizing furnace operations
✔ Reduce emissions and contribute to sustainability efforts
✔ Improve productivity with data-driven process control
✔ Stay ahead of regulatory changes related to industrial emissions
With DOE-backed initiatives supporting the shift toward energy efficiency, now is the time for manufacturers to integrate CelSian’s solutions into their operations.
Explore CelSian’s Cutting-Edge Solutions
CelSian continues to lead the industry with innovative technologies and training programs that drive efficiency in glass manufacturing. Learn more about their solutions here.